3D-tulostetun katamaraaniveneen valmistuksen alkuvaiheita
Suunnittelun lähtökohdat
Kulkuneuvon suunnitteluvaiheessa ensimmäisenä lähtökohtana huomioitiin käytössä olevan 3D-tulostuslaitteiston maksimitulostusalue, joka on 1.3 x 2.5 x 1 m. Tulostusalueen ollessa suhteellisen iso, mutta veneiden kokoluokka huomioiden kuitenkin suhteellisen rajallinen, päädyttiin valmistamaan aluksen runko useammasta osasta. Asiaa monelta kantilta suunnitellessa ja myös olemassa olevia veneratkaisuja tutkiessa päädyttiin ratkaisuun, että veneestä tehtäisiin kaksirunkoinen katamaraanivene ja runko-osat tehtäisiin pituussuunnassa kahdesta erikseen 3D-tulostettavasta osasta. Kuvassa 1 nähdään suunnitteluohjelmassa veneen neljä erillistä runko-osaa, jotka on pituussuunnassa jaettu esimerkiksi hirsirakentamisessa tunnetulla ”lohenpyrstöliitoksella”. Runko-osan kokonaispituus on n. 4.1 m. Katamaraanirungon osat suunniteltiin liitettäväksi toisiinsa alumiiniprofiilipalkeilla, jotka ovat helposti skaalattava ratkaisu. Pituussuunnassa kaksi katamaraanirungon osaa liitetään lohenpyrstöliitoksen lisäksi alumiiniprofiilipalkilla, joka toimii samalla myös jäykistävänä rakenteena pituussuunnassa. Alumiiniprofiilipalkeille suunnitellut asennusurat ovat havaittavissa kuvasta 1. Veneen katamaraanirungon osat suunniteltiin purjehduskatamaraanin rungon suunnittelusääntöjä mukaillen pienemmässä mittakaavassa.
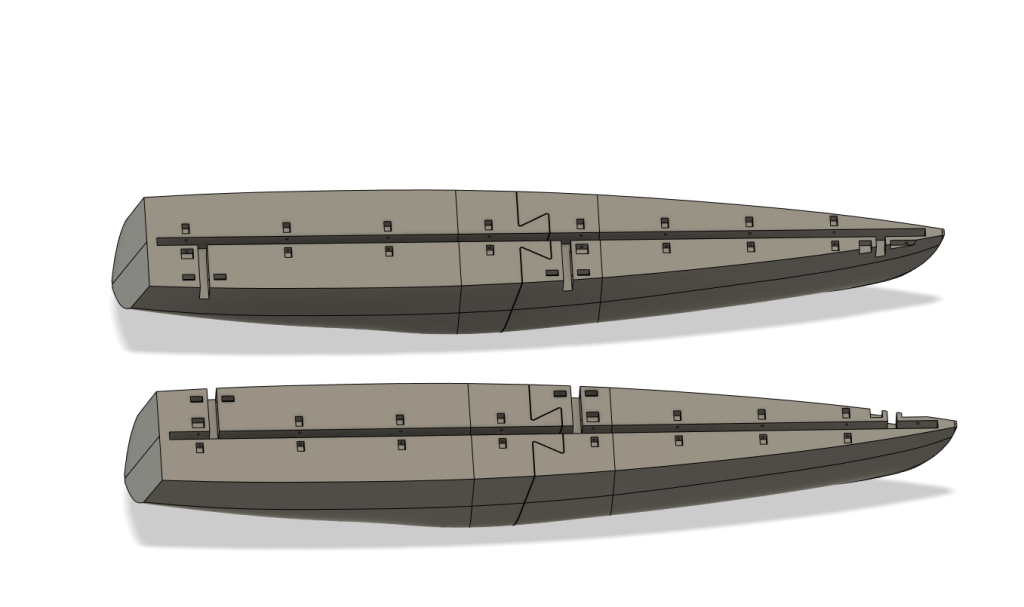
Kuva 1. Katamaraanivenerungon osat 3D-suunnitteluohjelmassa (Kuva: Eetu Huttunen)
Materiaalivalinta
Kun rungon osat oli suunniteltu, aloitettiin varsinaisten runko-osien valmistus. Materiaaliksi veneen runko-osiin valikoitiin selvitysten perusteella ASAGF20 komposiitti, koska rungon tiedetään altistuvan vedessä ollessaan haastaville olosuhteille. ASAGF20 on komposiittilaatu, joka sisältää ASA polymeerin lisäksi 20 % lasikuitua. ASA polymeeri on luja, iskunkestävä materiaali, joka sietää hyvin UV-säteilyä sekä muita ulkoilmaolosuhteita. Komposiittiin lisätty lasikuitu tuo lisää mekaanista lujuutta ja helpottaa 3D-tulostusta, koska kuitumateriaali pienentää tulostuksen aikaista kutistumaa. Materiaalivalintaa tehdessä oli havaittu myös, että kyseistä komposiittilaatua on hyödynnetty muualla maailmalla onnistuneesti 3D-tulostetun veneen runkomateriaalina. Tämä tieto tuki meidän materiaalivalintaamme yhdessä omien aikaisempien ASA materiaalin 3D-tulostuskokemuksien kanssa.
3D-tulostuksen aloitus
Aluksi ennen varsinaisten runko-osien valmistuksen aloitusta leikattiin suunnitteluohjelmassa mallista pieni osa lohenpyrstöliitoksen kohdalta, joka tulostettaisiin testiksi uudella materiaalilla. Liitoskohta päädyttiin tulostamaan oikeiden tulostusparametrien hakemiseksi sekä sen vuoksi, että voitiin testata liitoksen välystä oikeassa mittakaavassa. Kuvassa 2 nähdään 3D-tulostetut katamaraanirungon lohenpyrstöliitoksen testikappaleet. Katamaraanirungon osia tulostettaessa päädyttiin käyttämään 45 asteen 3D-tulostuspäätä, koska katamaraanirungon osista haluttiin tehdä sisältä ontot ja minimoida tämän avulla niiden massaa. 45 asteen tulostuskulma mahdollistaa onttojen rakenteiden tulostamisen ilman erillistä tukimateriaalia kappaleen sisällä. Kuvassa 3 nähdään käynnissä oleva tulostusprosessi, jossa tulostetaan katamaraaniveneen rungon osaa 45 asteen suuttimella. Rungon osia kokeiltiin aluksi tulostaa 2 mm:n tulostussuuttimella, joka osoittautui kuitenkin todella hitaaksi tavaksi yhden osan tulostamisen kestäessä noin 3 vuorokautta. Tämän vuoksi päädyttiin käyttämään 4 mm:n tulostussuutinta, jolloin tulostusaika tippui noin 32–36 tuntiin.
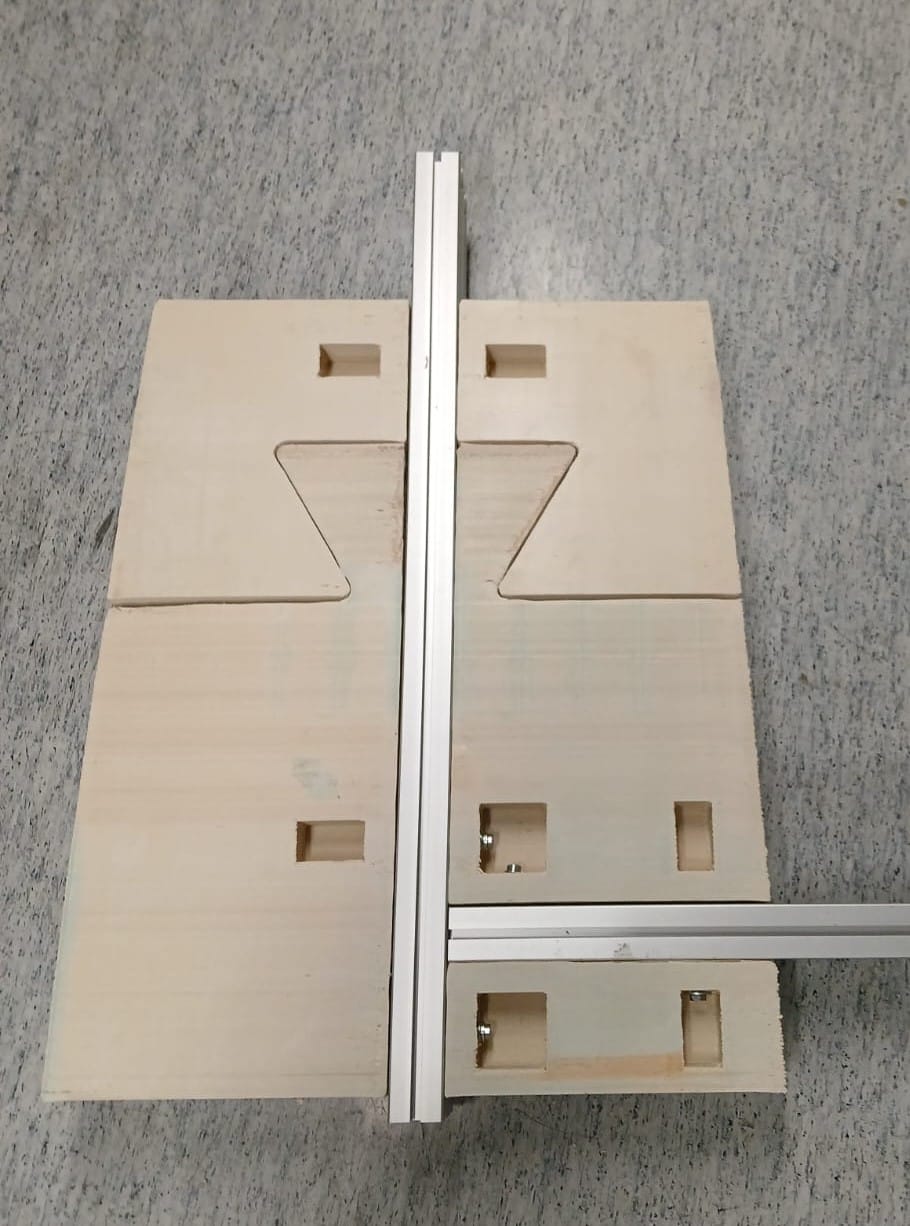
Kuva 2. Katamaraanivenerungon ”lohenpyrstöliitos” koekappaleet (Kuva: Eetu Huttunen)
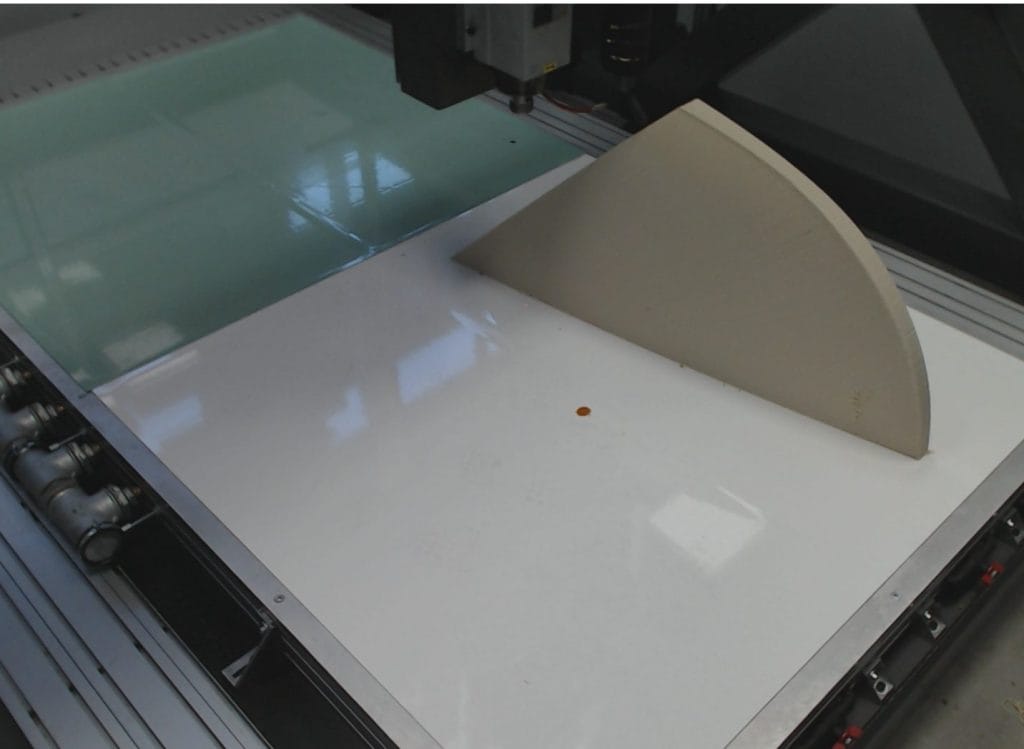
Kuva 3. Katamaraanivenerungon 3D-tulostusprosessi (Kuva: 3D-tulostimen omasta kamerasta.)
Haasteita ponttoneiden 3D-tulostuksessa
Kaikki ei kuitenkaan sujunut neljän runko-osan tulostuksessa täysin ongelmitta. Prosessissa haasteita aiheutti suhteellisen suuret tulostettavat kappaleet ja tämän vuoksi pitkät tulostusajat, tulostusalustojen ja tulostuspedin välisen vakuumiliitoksen pettäminen sekä tulostusmateriaalin liian voimakas tartunta tulostusalustaan. Pitkät tulostusprosessit itsessään ovat herkkiä ongelmille, koska tulostusajan kasvaessa myös todennäköisyys virheen sattumiselle jossain tulostuksen vaiheessa kasvaa. Varsinaisesti tulostuslaitteiston mekaniikasta tai virheistä johtuvia ongelmia ei ollut. Suurin vikatilanteiden aiheuttaja venerungon osien 3D-tulostuksessa oli lämmitettävän, alumiinisen tulostuspedin ja tämän päälle tulevan varsinaisen tulostusalustan välisen vakuumiliitoksen pettäminen kesken tulostuksen. Tämä aiheutti sen, että tulostettava kappale pääsi liikkumaan ja näin ollen tulosteet epäonnistuivat. Tämä tapahtui 6 kertaa kesken tulosteiden ja pahimmissa tapauksissa myös 45 asteen tulostussuutin katkesi sen törmätessä virheasennossa olleeseen tulostettavaan kappaleeseen. Lopulta tähän ongelmaan ratkaisuksi keksittiin varmistaa alustojen ja vakuumipedin välinen liitos hyödyntäen ohutta alumiinilistaa alustan reunaan kiinnitettynä, joka estää tulostusalustan mahdollisuuden liikkua vakuumialustan päällä. Lisäksi tulostusalustan reunat teipattiin alumiiniteipillä alustaan kauttaaltaan paremman kiinnipysymisen varmistamiseksi. Tämä ratkaisu todettiin toimivaksi ja loput tarvittavat katamaraanirungon osat saatiin tulostettua ilman alustan irtoamisongelmaa.
Alustan kokoonpano ja ensiuitto
Kun kaikki rungon osat oli tulostettu, oli aika aloittaa rungon osien kokoonpano. Rungon liitosta varten hankittiin alumiiniprofiilipalkit sekä tarvittavat kiinnikkeet. Tulostettuja rungon osia työstettiin hiomalla hiukan lohenpyrstöliitoskohdista sekä alumiiniprofiilien kiinnitysurista. Lisäksi kiinnitysreikien kohdat työstettiin poran avulla, jotta kiinnityspultit varmasti sopivat paikoilleen. Tämän jälkeen katamaraanirungon osat liitettiin ensin lohenpyrstöliitoksen avulla toisiinsa ja sen jälkeen alumiiniprofiilipalkkien ja pulttiliitoksien ja kulmakiinnikkeiden avulla toisiinsa (kuva 4). Katamaraaniveneen runkoa haluttiin kokeilla vedessä tässä vaiheessa, jotta varmistutaan sen toimivuudesta ennen varsinaisten kansirakenteiden suunnittelua ja valmistusta. Koeuittoa varten päädyttiin leikkaamaan rungon päälle suunnitellun muotoinen pohjalevy jämäköistä 24 mm:n vahvuisista vanerilevyistä. Lisäksi keulaan kiinnitettiin trailerointia sekä veneen käyttöä helpottavat lenkit köysille. Katamaraanirungon toimivuutta ja kellumista sekä kantavuutta haluttiin tässä kohtaa testata järvellä, joten päädyttiin suorittamaan ensimmäinen koeuitto veneelle ilman moottoria. Koeuitolla havaittiin, että vene kelluu hyvin ja sekä kantavuutta että tukevuutta on rungossa riittävästi. Kuitenkin ensimmäisellä uitolla veneen kelluessa havaittiin tarkistusluukuista ponttoonien sisälle tihkuvan hiukan vettä. Todennäköisesti vesi tihkui 3D-tulostuksessa syntyvistä kerroksen aloituskohdista, joihin on mahdollisesti jäänyt hyvin pieniä huokoisia kohtia sekä mahdollisesti myös joidenkin tulostuskerrosten väleistä. Tämän vuoksi päätettiin, että ponttonit tultaisiin pinnoittamaan ekologisella TKR vedeneristysaineella. Kuvassa 5 on esitettynä katamaraaniveneen runko-osa ensimmäisellä koeuitolla Savonlinnassa.
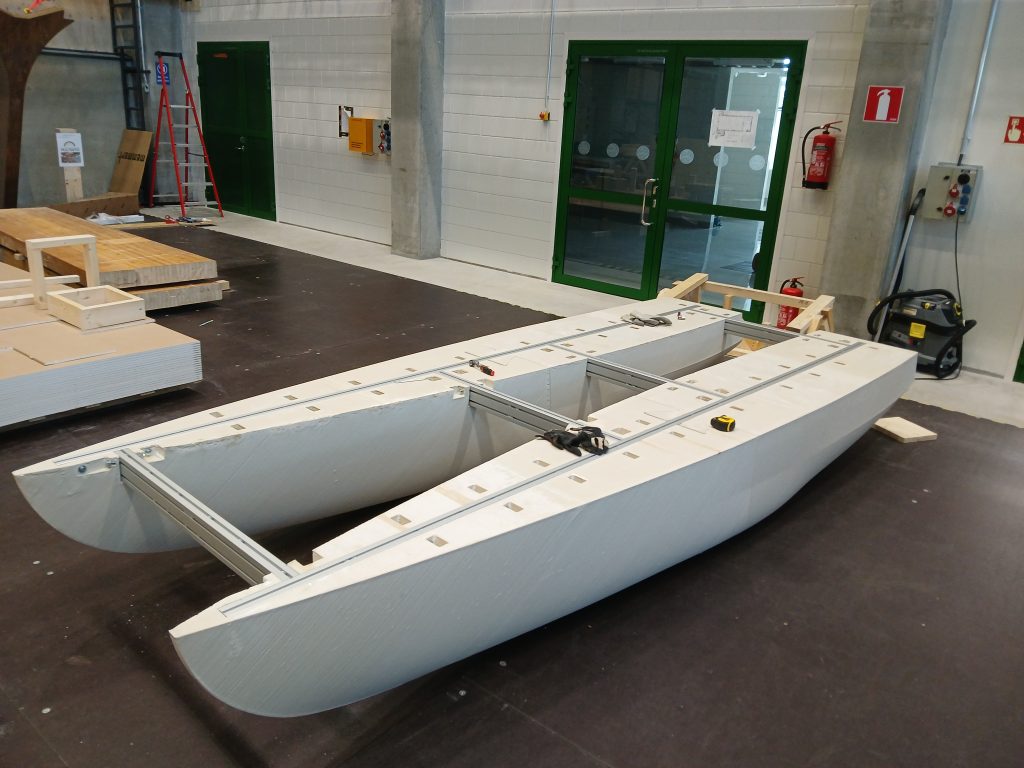
Kuva 4. Katamaraaniveneprototyypin runko-osien liittäminen toisiinsa (Kuva: Eetu Huttunen)
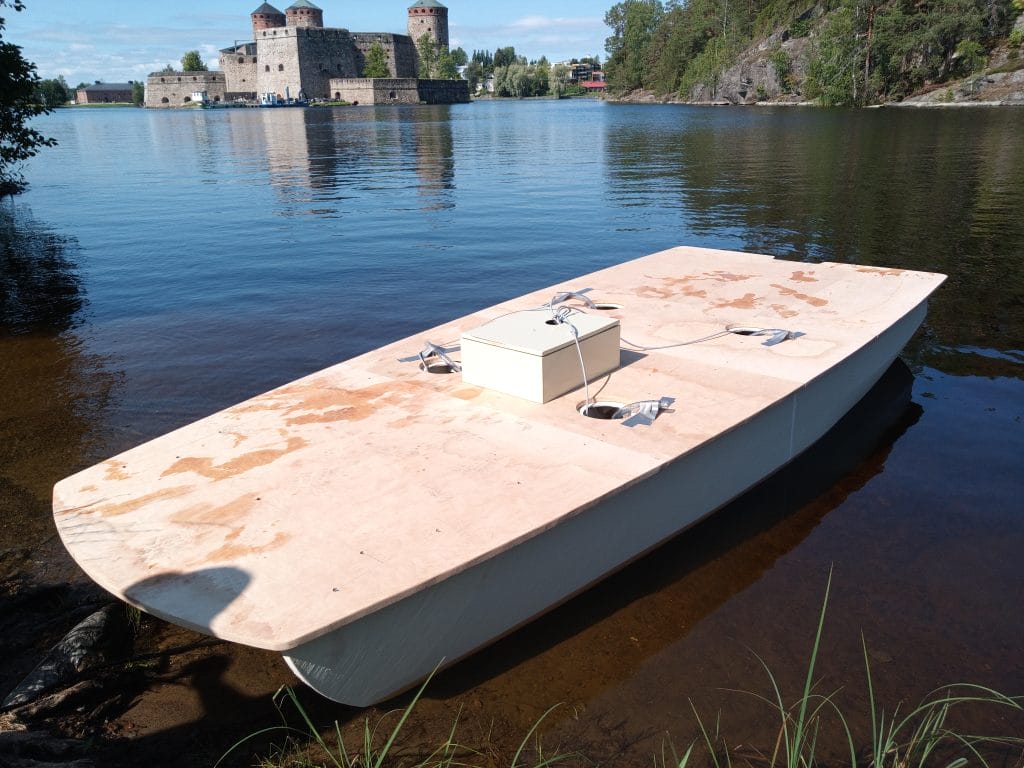
Kuva 5. Katamaraaniveneprotyypin ensimmäinen koeuitto (Kuva: Mikko Nykänen)
Jatkosuunnitelmat
Kulkuneuvon voimalähteeksi on kaavailtu noin 3 kW tehoista sähköperämoottoria. Katamaraanirungon ohjattavuus yhdellä moottorilla voi osoittautua haastavaksi ja tämän vuoksi ennen tehokkaan sähköperämoottorin hankintaa halutaan varmistaa veneen toiminta ja ohjattavuus vedessä. Kokeilussa käytetään 5 hp polttomoottoriperämoottoria, joka vastaa teholtaan noin 3 kW:n sähköperämoottoria. Tämän testauksen avulla voidaan varmistaa veneen oikeanlainen toimivuus vedessä, moottorin tehon riittävyys sekä ohjattavuuden toiminta. Kun koeajo moottorin kanssa on suoritettu, voidaan tehdä lopullinen moottorivalinta sekä aloittaa kansirakenteiden suunnittelu sekä toteutus. Veneen kansirakenteissa kokeillaan hyödyntää erilaisia biokomposiittimateriaaleja. Myös akustoja sekä lataukseen tarvittavia aurinkopaneeleja sekä lataussäätimiä voidaan alkaa suunnittelemaan ja mitoittamaan yhdessä muun veneen sähköjärjestelmän kanssa. Projektin etenemistä tullaan seuraamaan vastaavanlaisten artikkeleiden muodossa myös jatkossa!
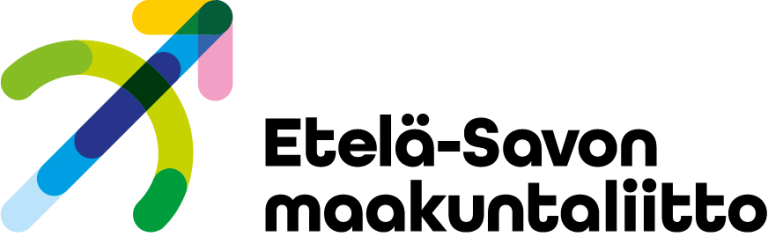
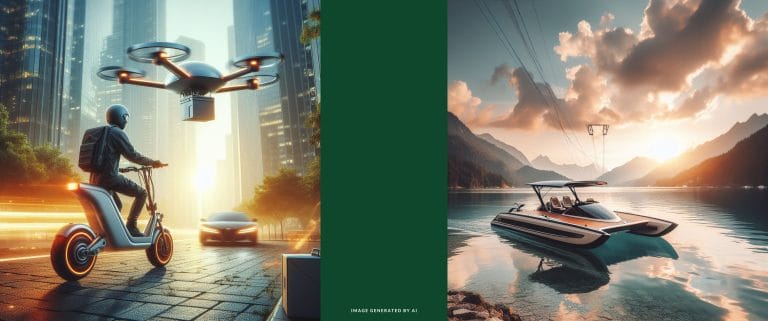